Scaling Up Innovation -The OxyMem Journey
OxyMem is now facing into its third year.
Having recently opened an office in the United States to service the growing demand in the North American market we decided to take a step back and think about how far we have come since we started up. In doing so, we spoke to John Geaney, OxyMem’s Manufacturing Manager about the challenges faced in developing a manufacturing process from a lab scale protype into a full scalable, shift based production process which is in place today.
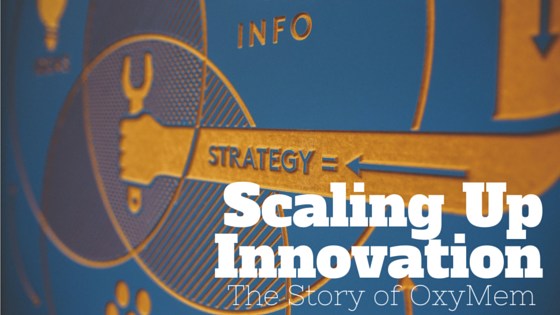
The OxyMem production facility is based in Athlone, Co. Westmeath in the Irish Midlands. John explains that one of the most attractive reasons for basing OxyMem here was for its long history of polymer technologies in the area.
“We secured great people with experience on board at an early stage and after initial training, we successfully managed to bring the initial line to a higher stage of production. This has remained a constant focus of the operation here and every month we have learned something new about the process, the equipment and the materials we are using. This has allowed us to make incremental improvements to either the speed of production or the quality of the membranes we are producing.”
We are incredibly proud of our fantastic team at OxyMem. A workforce of high quality, adaptable and flexible people who learn quickly and diligently. John explains that it’s not an easy job when nobody has built the product before and when changes are being made quickly and frequently.
“In the 20 months of operations, we have designed and manufactured nearly every key piece of equipment to suit our own unique circumstances. Having to develop solutions from first principles is a constant at OxyMem. We have no need to remind ourselves that this is a novel, disruptive and innovative technology. By definition therefore, nobody has done this before and we have to regularly figure out our own solutions and quickly develop them to permit us to move to a high speed, highly repeatable process.”
With every day comes change and innovation. Levels of control and checks have been added as the company has grown. Throughout most of 2014, OxyMem ran a single cycle shift and shut the entire factory down every evening. “Today we run a 24 Hours, 3 cycle shift, 5 days a week, maintaining control of our processes over this extended period of operation has required us to learn about the capabilities of our processes quickly.”
So, what does the future hold for OxyMem? “2016 will be about adding more lines, higher speed of production, automation and reducing defect opportunities. Our customers can expect a robust Quality Management System and for us to achieve ISO 9000 and ISO14000 certification – giving us the assurance that we are achieving sustainable manufacturing processes and procedures.”
In a once disused factory in the Irish Midlands, a vibrant and thriving new company has sprung and is busier than ever before. As the company continues to grow, John and the rest of the team look forward to continuing to adapt, innovate and deliver.